Avoiding Downtime: How to Get the Right Equipment at the Right Time
In construction, every day counts. Equipment delays can disrupt your schedule and cost thousands in idle labor and lost productivity. Learn how to avoid downtime and keep your projects on track with reliable, on-demand equipment access through Downstream Marketplace.
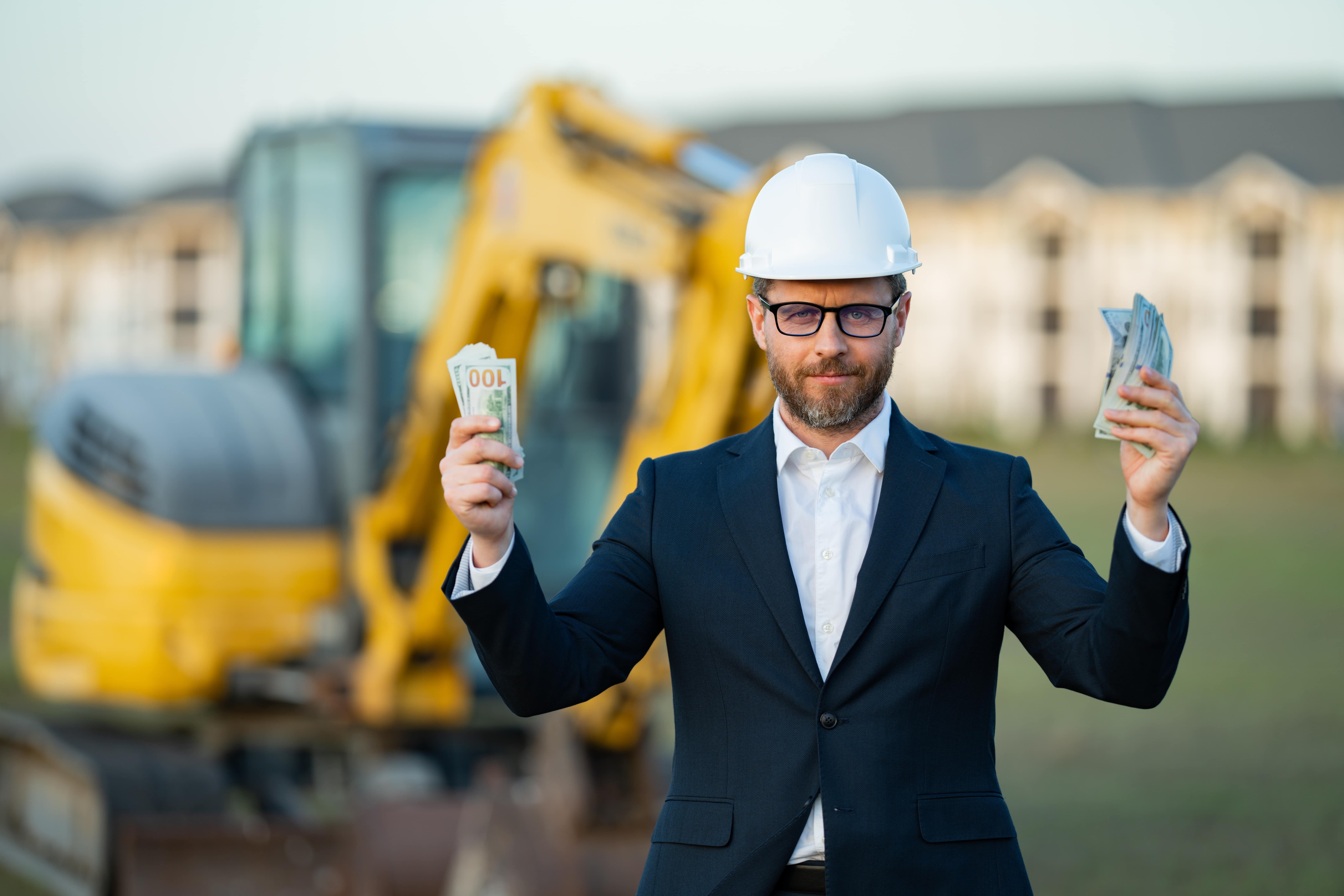
In the home building industry, downtime—periods when construction activities halt due to unavailability of necessary resources—can significantly impact project timelines and budgets. A comprehensive study by McKinsey & Company revealed that large construction projects typically run 20% longer than scheduled and incur 80% more costs than originally planned.
Key Contributors to Downtime:
- Equipment Shortages: Delays in procuring essential machinery.
- Equipment Failures: Breakdowns due to inadequate maintenance.
- Resource Constraints: Insufficient allocation of labor and materials.
A report by Plan Academy highlights that resource constraints, including equipment shortages, are a leading cause of schedule delays, affecting approximately 30% of construction projects worldwide.
The Financial Impact of Downtime
Downtime not only delays project completion but also escalates costs. The Construction Industry Institute (CII) identifies late deliverables, including equipment, as a significant risk factor leading to project delays.
Financial Implications:
- Increased Labor Costs: Paying workers during idle periods.
- Extended Overhead Expenses: Prolonged site management and supervision.
- Penalty Fees: Fines for not meeting contractual deadlines.
Strategies to Mitigate Downtime
To minimize downtime, home builders can implement the following strategies:
- Proactive Equipment Planning: Anticipate equipment needs and schedule rentals or purchases in advance.
- Regular Maintenance: Ensure all machinery undergoes routine checks to prevent unexpected failures.
- Utilize Equipment Marketplaces: Leverage platforms like Downstream Marketplace to access a broad network of equipment suppliers.
How Downstream Marketplace Ensures Reliable Equipment Access
Downstream Marketplace connects home builders with a vast network of equipment suppliers, offering:
- Real-Time Inventory Access: View current equipment availability to make informed decisions swiftly.
- Transparent Pricing: Compare rates across suppliers to find cost-effective options.
- Flexible Rental Terms: Choose rental periods that align with project timelines, reducing unnecessary costs.
By utilizing Downstream, builders can ensure they have the right equipment precisely when needed, thereby minimizing downtime and keeping projects on schedule.
Scenario: Preventing Costly Downtime with Downstream Marketplace
A home builder is working on a 30-home subdivision and is in the critical site preparation phase. During excavation, the project’s only excavator unexpectedly breaks down. The crew cannot proceed with grading and trenching, which causes the entire project to come to a halt.
The builder contacts their usual equipment supplier, but the supplier informs them that a replacement excavator won’t be available for five days. Without the excavator, multiple trades are affected, leading to idle crews, delayed schedules, and mounting costs.
The builder estimates that each day of downtime will cost:
- Idle Crew Costs: $5,000/day – Labor costs for heavy equipment operators, site supervisors, and subcontractors who can’t proceed.
- Extended Equipment Rental Fees: $1,500/day – Fees for other rented machinery, such as skid steers and compactors, that sit unused.
- Overhead Costs: $500/day – Project management, site utilities, and general expenses.
Total Estimated Loss per Day: $7,000/day
If the builder waits for their usual supplier, the five-day delay could result in:
$7,000/day × 5 days = $35,000 total loss.
Solution: Downstream Marketplace to the Rescue
Instead of waiting for their usual supplier, the builder turns to Downstream Marketplace. Within minutes, they find a nearby supplier with an available excavator and arrange for next-day delivery.While the expedited rental and delivery cost $5,000, the builder effectively cuts the downtime from five days to just one day, minimizing the financial impact.
Outcome: Significant Cost Savings and Project Back on Track
By leveraging Downstream Marketplace, the builder avoids four additional days of downtime. The breakdown of the cost savings is as follows:
- Downtime Cost for One Day: $7,000
- Equipment Replacement Cost: $5,000
Total cost for one day of downtime: $12,000
If the builder had waited for their usual supplier, the five-day delay would have cost $35,000. Thanks to Downstream, the builder’s net savings is $23,000—a huge reduction in downtime-related losses, keeping the project on schedule and protecting the bottom line.
Conclusion
Downtime poses a significant threat to the efficiency and profitability of home building projects. By understanding its causes and implementing strategic solutions—such as leveraging platforms like Downstream Marketplace—builders can mitigate risks, control costs, and ensure timely project completion.
Read similar blogs
-min.webp)
Subscribe to get helpful business insights
Quis nostrud exercitation ullamco laboris nisi ut aliquip ex ea commodo consequat. Duis aute irure dolor in voluptate.