Making the Most Out of Tenant Improvements: Key Areas to Focus On and the Equipment You’ll Need
Tenant improvements—often abbreviated as TIs—are a cornerstone of commercial real estate construction. Whether you’re customizing an office suite for a new lease, retrofitting a retail space, or modernizing an outdated interior, tenant improvement projects require precise coordination across trades, timelines, and budgets. Getting the job right means more than just finishing on time. It’s about delivering a space that’s functional, safe, and aligned with the tenant’s vision. In this post, we’ll break down the key areas that are most important to nail in a TI project and highlight the critical construction equipment that helps ensure success.
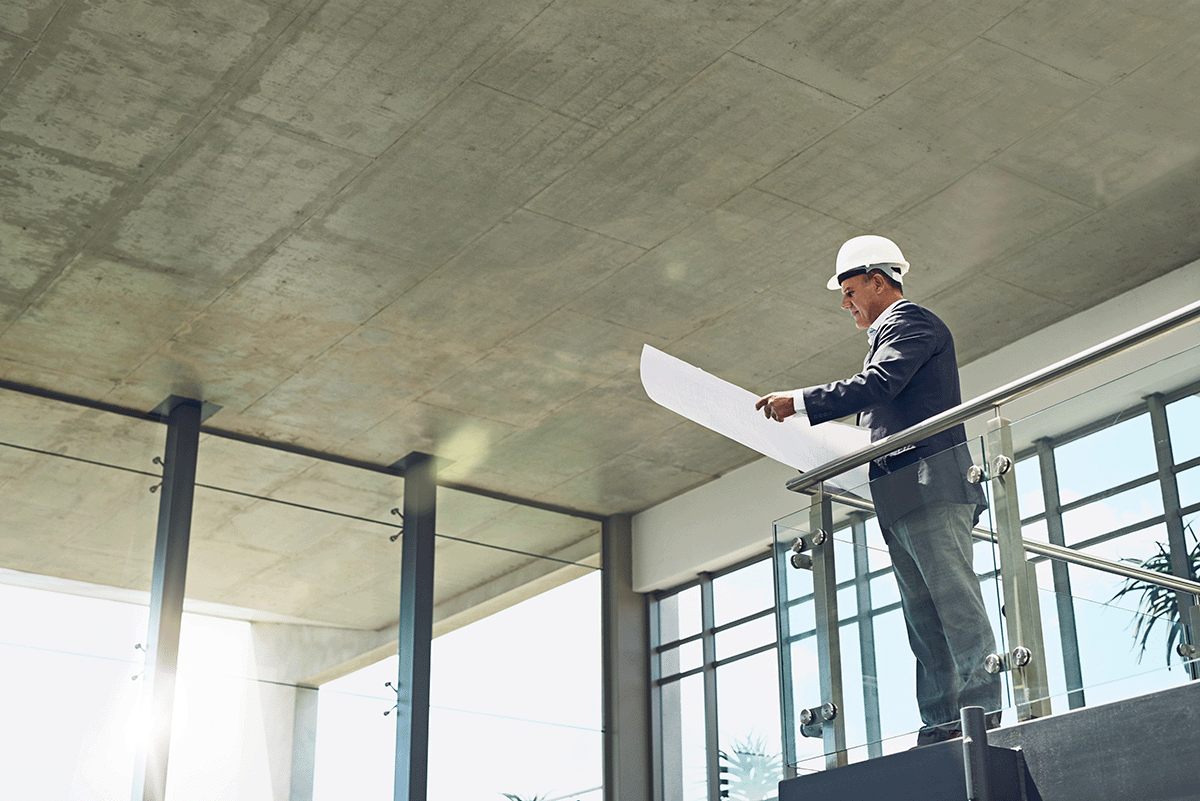
What Are Tenant Improvements?
Tenant improvements are modifications made to a commercial space to meet the operational or aesthetic needs of a tenant. These can range from basic finish updates like flooring and paint to more complex work such as new HVAC systems, plumbing relocations, electrical upgrades, and even structural changes.
Unlike ground-up construction, TI projects usually occur within the constraints of an existing building. That means teams must work around existing MEP systems, building codes, lease agreements, and sometimes even ongoing business operations. Time is often tight—tenants don’t want to pay rent on unusable space—and the margin for error is small. Careful planning, experienced labor, and the right tools for each stage of the job are crucial.
1. Demolition and Site Preparation: Starting with a Clean Slate
Every successful build-out begins with efficient demolition. Whether you’re removing outdated cubicles, tearing out old flooring, or gutting entire interiors, demo work sets the tone for everything that follows. It needs to be done safely, cleanly, and quickly to maintain project momentum.
Because TI projects typically take place indoors, contractors need equipment designed to minimize disruption. Concrete saws and jackhammers help break down old materials, while dust control vacuums, negative air machines, and sealed containment zones keep the jobsite clean and code-compliant. For hauling debris, compact dumpers or walk-behind carriers are ideal for navigating narrow hallways or elevators common in commercial buildings.
Noise and dust mitigation is especially important in partially occupied buildings, where tenants may still be working nearby. Electric demolition tools are often preferred over gas-powered alternatives to reduce noise and eliminate harmful exhaust.
2. Framing and Drywall: Creating the Canvas
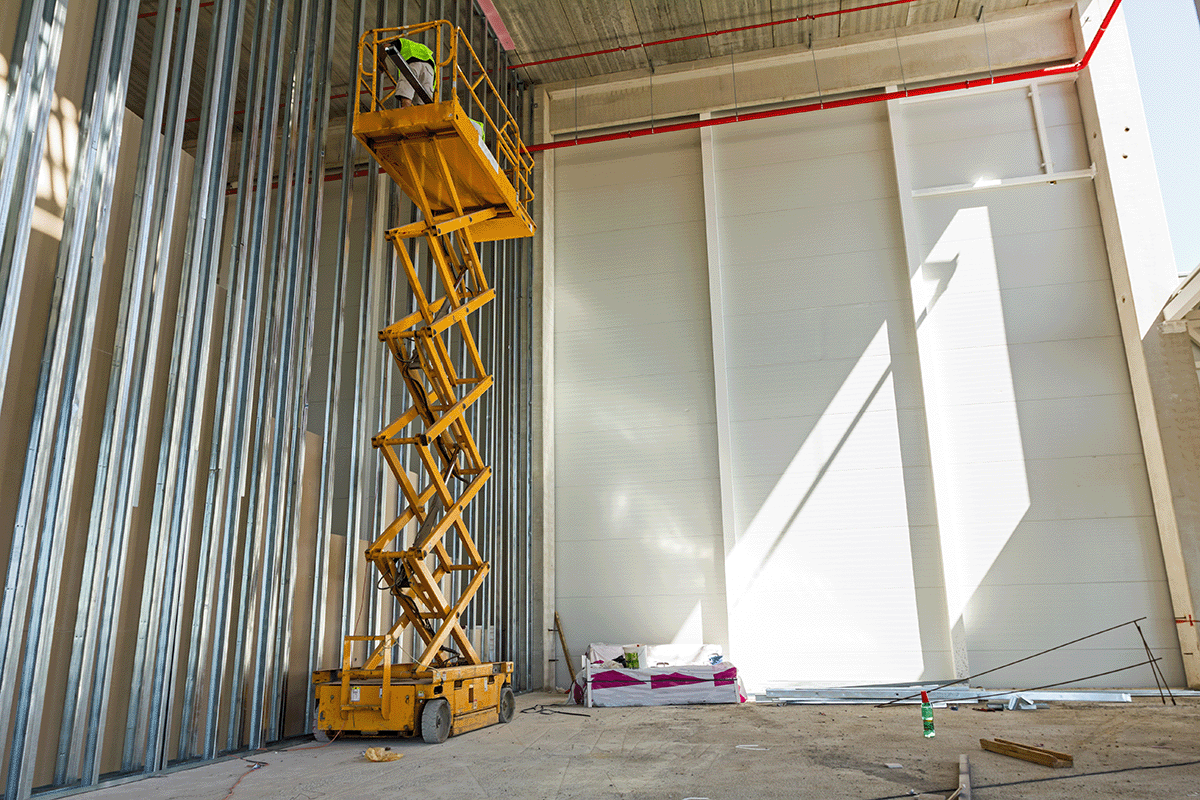
Once demolition is complete, the space begins to take shape during the framing and drywall stage. This is where walls, partitions, and ceiling grids are installed based on the new floorplan. Precision is everything—improper measurements or off-level framing can create problems that cascade into other trades, from electrical layouts to cabinetry installs.
Drywall lifts and material lifts are vital for handling heavy sheets safely and efficiently, especially in spaces with tall ceilings. Laser levels help ensure framing is straight and square, while cordless impact drivers speed up assembly without being tethered to power cords. If the project involves high walls or ceiling work, mobile scaffolding or compact scissor lifts allow teams to work comfortably and safely.
Because this phase often involves coordination between framers, electricians, and HVAC teams, having the right equipment on hand minimizes downtime and keeps the project on schedule.
3. Electrical and Lighting: Powering the Vision
Electrical upgrades are among the most technical components of a tenant improvement. Modern workspaces demand smart lighting, extensive power access, and high-speed data infrastructure. From relocating outlets to installing LED panels or emergency lighting, these systems must be installed with both compliance and efficiency in mind.
Cable pullers and fish tapes make routing wires through walls and ceilings easier, while cordless drills and power saws improve productivity in tight spaces. Step ladders or A-frame ladders provide access to ceiling tiles and light fixtures, and temporary portable lights keep the workspace illuminated if permanent fixtures aren’t yet live.
When working in existing structures, electricians often encounter unmarked circuits or outdated wiring. That’s why diagnostic tools like circuit testers, multimeters, and voltage detectors are essential for both safety and code compliance.
4. HVAC and Plumbing: Upgrading Comfort and Compliance
Whether it’s adding a breakroom, expanding restrooms, or rerouting ductwork for better airflow, mechanical upgrades are common in tenant improvements. These systems are often hidden behind walls and ceilings, but their performance directly affects tenant satisfaction and building efficiency.
HVAC upgrades may include installing new air handlers, thermostats, or diffusers. For this, you’ll need ladders, duct lifters, and sometimes compact cranes or hoists. In tight ceiling cavities, maneuverable lifts can be a game-changer for worker comfort and productivity.
Plumbing upgrades—especially in kitchenettes or bathrooms—require pipe cutters, threaders, core drills, and water testing equipment. Wet/dry vacuums help manage water during installations or emergency shutoffs, while air pressure testers ensure systems are leak-free before final inspections.
Energy efficiency is also an increasing priority. According to the U.S. Energy Information Administration, HVAC alone accounts for nearly 30% of energy use in commercial buildings—so making smart upgrades here can pay dividends long after the project is complete.
5. Flooring and Finish Work: Where Design Meets Durability
The flooring stage is often the first point at which the space begins to resemble the finished vision. Whether the design calls for luxury vinyl plank (LVP), polished concrete, commercial carpet, or ceramic tile, each material has its own preparation and installation requirements.
Old adhesives, grout, or uneven slabs must often be removed using floor grinders or scrapers. For tile work, wet saws and spacers ensure clean cuts and straight lines. Carpet installation may require tack strips, stretchers, and seam rollers. For all finishes, it’s important to maintain a clean and climate-controlled environment, especially when adhesives or finishes need to cure properly.
Fans and dehumidifiers can accelerate drying times and prevent moisture-related issues like bubbling or peeling. Keeping the environment stable helps trades like painters and finish carpenters work more efficiently, reducing punch list items down the road.
6. Painting and Design Details: Making It Feel Complete
Paint is often the final touch—and one of the most visible elements—of a tenant improvement project. A quality paint job requires both prep and precision. That means protecting newly installed finishes, sealing imperfections in drywall, and applying clean, even coats of color that match the tenant’s brand aesthetic.
For large areas, airless sprayers deliver speed and consistency. Painters also rely on ladders, rollers, and drop cloths, while negative air machines or air scrubbers help reduce lingering odors from VOCs (volatile organic compounds) during and after application.
Accent walls, signage installations, or branded murals may also be part of the final design, and completing these details smoothly depends on having the right finishing tools and access equipment on site.
Why Downstream Is Your Ideal Equipment Rental Partner
Tenant improvement projects often involve multiple trades working on top of one another in a confined timeline. That makes reliable equipment availability and seamless logistics critical.
At Downstream, we make it easier to keep your TI projects moving. Our rental platform gives you access to a wide selection of construction equipment—from drywall lifts and floor grinders to pipe threaders and dust control solutions—all with just a few clicks. We offer:
- On-demand rentals for short-term or long-term projects
- Transparent pricing so you know what you’re paying upfront
- Real-time delivery tracking to keep your crew on schedule
- Equipment variety tailored to commercial build-outs and tenant work
Whether you’re a general contractor or a specialty subcontractor, Downstream helps eliminate downtime and streamline jobsite logistics so you can focus on quality and delivery.
Final Thoughts: Build Better, Smarter, and On Time
Tenant improvements are more than just construction—they’re an investment in how people work, shop, and live. By focusing on the most critical aspects of your project and equipping your team with the right tools, you can consistently deliver results that tenants and building owners will appreciate.
Ready to streamline your next tenant improvement project? Get started with Downstream and experience how simple and efficient equipment rentals can be.
Read similar blogs
-min.webp)
Subscribe to get helpful business insights
Quis nostrud exercitation ullamco laboris nisi ut aliquip ex ea commodo consequat. Duis aute irure dolor in voluptate.